While today’s supply chain challenges remain a pressing issue for companies of all types, perhaps no other industry feels them more acutely than the life sciences—where bottlenecks and disruption could literally mean life or death for patients. From disruptions dating back to the start of the COVID-19 pandemic to ongoing quandaries regarding the sustainability and scalability of existing processes, Business Talent Group has seen growing demand from organizations to address issues at every step of the supply chain.
To help life science leaders address these critical issues, we’ve turned to supply chain operations expert Marcos Buelvas. Read on for a closer look at what’s going on at the ground level in life science supply chains—as well as Marcos’s recommendations on how organizations can create more agile and resilient operations that keep the production of life-improving treatments on track.
Meet The Expert
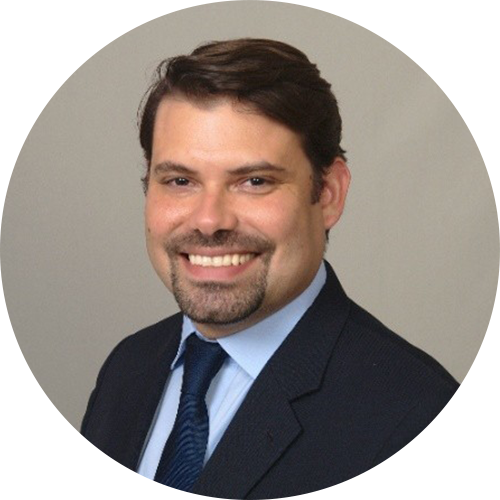
Marcos Buelvas
Marcos is a hands-on leader with experience designing and implementing manufacturing and supply chain transformation efforts and leading cross-functional manufacturing and supply chain programs for well-known global brands.
How has supply and demand in the life sciences been impacted in the last few years?
Similar to every other industry, COVID and other disruptions have had a significant impact. On the demand side, demand for many pharmaceutical products—specifically vaccines, of course—went up a great deal. But the demand for other common over-the-counter products, such as cold medicines, also went up. New and repurposed therapies went into the market and found new therapeutic applications. The distribution of super low temperature products like the new vaccines meant an increase in that particular cold chain, and more importantly, its reach to end consumers and patients around the world.
On the supply side, we experienced constraints in all sorts of products, from saline solution to life saving drugs. It was quite widespread to find constraints not just in production capacity but also in distribution capacity. The benefit of this has been tighter coordination across the supply chain and finding new ways of working together across functions, geographies, and companies (e.g. suppliers).
Structurally, it is clear that risk is (and should have always been) a major driver of decision making. Decisions around dual supply, near-shoring, and localized capacity have become part of everyone’s language and should stay there so that we are better prepared to manage known and unknown risks, and appropriate plans should always be detailed and understood within and across organizations.
Which supply chain and manufacturing model makes the most sense for life science companies in today’s environment (e.g. minimum cost, maximum throughput, highest yield, zero environmental impact, or one based on a combination of multiple factors)?
Supply chain is always a combination of several factors. It is becoming increasingly clear that none of those variables will sustain us in the long term if we don’t account for de-risking the supply chain, so a lot of emphasis is going toward supply chain models that incorporate risk, business continuity, resilience, and flexibility.
There is no question that the market remains competitive and will remain so because we have to continue to reach increasing consumer and patient populations. Hence, it is imperative that the cost and asset focus also remain; but it is clearer than ever that multi-dimensional optimization is a must.
Where are the biggest challenges and bottlenecks in life science supply chains at present and how are the most effective organizations addressing them?
It is clear that resilient supply chains will win, and we are not there yet. So, the challenge is to fight fires (they have increased) and build your future supply chain simultaneously. The future supply chain is necessary because, for example, low cost is not good enough anymore. That has to be supplemented with de-risked, etc.
For a long time, we have been pushing organizations to build more connected or integrated supply chains (pick your term) and this is the only vehicle to achieve fighting fires and build the future at the same time. The reason is simple, connected supply chains achieve the essence of supply chain which is to really understand how the links across the chain are working together and not independently so that teams are not spending all of their time inefficiently collaborating.
How can companies monitor and anticipate changes in demand to adapt supply chains and manufacturing in advance?
There are two critical connections for supply chain organizations, and they are the connections to Commercial organizations and to R&D in the context of product launches and future platforms. Strong linkages with these two organizations empower Supply Chain leaders to attain a better picture of demand as well as the attributes and assumptions of that demand forecast and its likely change or volatility. These linkages cover the three dimensions of robust people, processes, and technology to yield solid connectivity to demand and changes in it.
Perhaps most important to highlight is that the linkages cannot be taken for granted. Often, we say, “oh yes, we have a demand review process,” or “we have an S&OP process.” Unfortunately, we are not challenging the process, assumptions, and how real-time the information is connected for action across the organization to really stay ahead of demand—and that is the only way to do so.
What effect will cost pressures have on how organizations approach their supply chain and manufacturing operations?
For this area, I would primarily highlight the impact on the Sourcing and Procurement groups within Supply Chain organizations. Inflation has driven costs up anywhere from 10 to 50% across many items, and spikes could be even worse. Managing this volatility has been really hard for supply chain teams. The emphasis on agile procurement practices will increase and teams will be forced to integrate these practices along with shorter cycles on supplier contracts and off-contract purchasing. We have seen many suppliers directly advising their customers that they can’t honor existing contracts. In these circumstances, buyers are constantly engaging the market to understand supply constraints, substitution, and any opportunity they can get to control cost.
Until things stabilize more, there is no substitute for agile, active management of the sourcing and procurement environment, and more broadly across the end-to-end supply chain
What are some of the most effective digital tools to help optimize supply chain processes? How should companies think about the implementation of these tools?
Every digital innovation is being applied or studied in some form across supply chains; e.g., block chain is getting a lot of attention in Smart Contracts (Sourcing), Artificial Intelligence (AI) is changing Planning by offering more informed scenarios that incorporate learning and real time information, The Internet of Things (IoT) is enabling detailed tracking across manufacturing and supply chain nodes. The list goes on, but none of it can be belittled. It is all quite transformational, accretive, and can enhance some aspects of supply chain.
Beyond these technology applications, the idea of Control Towers is perhaps the most compelling. A supply chain requires a connected nerve-center with clear visibility across nodes, partners, manufacturing, etc. Creating this distributed, yet integrated visibility is no small task and requires robust processes and technology to connect diverse information. The value proposition is visible in top and bottom-line results given remarkable enhancements to supply chain responsiveness.
Implementation requires proven methodology and experienced teams. Above all, teams have to be dynamic and adaptable to engage and recognize that they will have to solve problems along the way to design and run the implementation program.
What role is AI playing in supply chain today and how do you see that evolving in years to come?
I am not overreaching when I say that it is everywhere. AI is about evaluating multiple data sources and providing options or recommendations on the decisions to be made. The role of AI is hence quite applicable to all aspects of the supply chain. For example, in Procurement, teams are using AI to evaluate supplier performance and recommend the best supplier based on location, performance, and/or cost adherence. These evaluations can take too long to be performed at scale without AI.
Another good example is Planning. Teams must plan production and inventory levels to support demand and are now incorporating new variables through AI to inform the decisions. There are great examples of incorporating weather, economic changes, inflation—among other variables—into models that provide options and recommendation on what we call Planning Targets.
We will continue to see increasing levels of investment year-on-year because the examples are more clearly demonstrating ROI.
What are the most important things for companies to keep in mind as they shift from strategic supply chain initiatives into implementation?
There is a lot to be said here, but in the interest of time and readability, I’ll just pick a few highlights:
- Keep it specific and practical and not general and conceptual. Think through the details. It’s not enough to say that you want to employ global sourcing strategy; for implementation, one must specify the components, the countries, and the suppliers, etc.
- Ensure top executive sponsorship for the strategy execution to ensure it yields good results. Multiple studies by top management consulting firms have shown an increase in results to the tune of 50% to 60% higher when the CEO is involved in implementing a supply chain strategy.
- Ensure that key stakeholders communicate and act like a team, despite the business function conflicts that may arise due to conflicting KPIs. Discussion among business units to support the strategy and to benefit the organization as a whole is the key.
- Understand the value of technology. Technology enabled tools could significantly enhance the performance of the supply chain by enabling decision making. But these technology-enabled tools can’t replace broken processes. So, while implementing the strategy for deployment of a technology, process improvement should be considered first to realize the expected benefits.
What makes independent supply chain experts like you an effective solution for companies seeking to strategically improve supply chain resilience and avert disruptions?
Independent supply chain experts like myself bring a wealth of diverse experiences that can supplement those of our clients. It is critical that experts not only bring knowledge, but a great deal of respect and appreciation for how to integrate and work as part of the client team. Beyond that, your expectation of any consultant is that they will value you, the client, and be committed to working hard to achieve the vision of success and enhance it however possible.
In the context of supply chain resilience this translates into carefully thought-through design principles that can be implemented and cost effectively sustained. It starts with how the organization sources and who it partners with in that space to reduce risk. For example, where are our sources of supply and are we monitoring this rigorously? It then extends to our manufacturing strategy, both internally and with external partners. And it ends with distribution and how we ensure we can meet customer and patient expectations. Inventory strategies are critical in this respect also and can make all the difference to ensure patients get their most needed medicines.
Explore your options to fine-tune your life science operations practices with Business Talent Group.
Whether you’re looking to recover from recent supply chain disruptions, prevent them from happening in the future, or improve your existing processes, you can find highly-skilled life science operations talent at Business Talent Group.
Business Talent Group’s network includes 4,600+ independent life science consultants, subject matter experts, boutique firms, project managers, and executives. Our talent have advanced degrees, specialized expertise, traditional consulting training, and hands-on experience. We serve:
- 13 of the top 15 largest pharmaceutical companies
- 6 of the top 10 biotech companies
- 8 of the top 10 medical device companies
See why more than 50% of the Fortune 100 and hundreds of other leading companies trust BTG to curate, vet, and compliantly deliver talent who fuel growth, innovation, and performance improvement.
GET THE SKILLS YOU NEED
Thousands of independent consultants, subject matter experts, project managers, and interim executives are ready to help address your biggest business opportunities.